What is Anodized Aluminum?
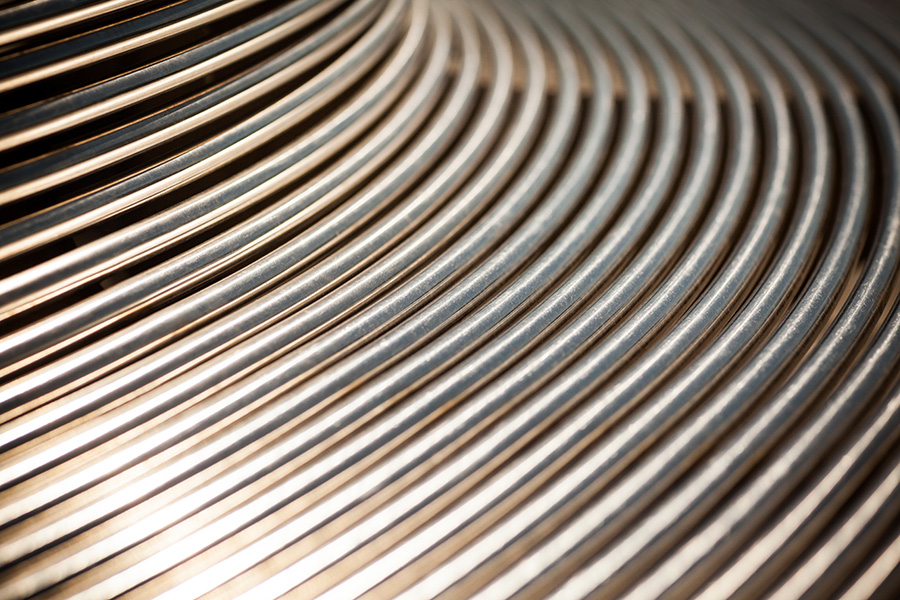
Introduction
Anodized aluminum is a process by which aluminum is treated to create a durable, corrosion-resistant surface. This process involves immersing the aluminum in an electrolytic solution and passing an electric current through it. As a result, an oxide layer forms on the surface of the aluminum, known as the anodic layer. This layer is integrated with the aluminum substrate, providing enhanced properties such as increased hardness, scratch resistance, and corrosion resistance.
The significance of anodized aluminum spans across various industries due to its unique properties:
- Architecture: Anodized aluminum is widely used in architectural applications for building facades, window frames, and roofing systems. Its durable finish withstands harsh weather conditions and UV exposure, maintaining its appearance and structural integrity over time. Additionally, the range of colors available through anodizing allows architects and designers to achieve desired aesthetics while ensuring longevity.
- Automotive: In the automotive industry, anodized aluminum is utilized for exterior trims, wheels, and engine components. The lightweight nature of aluminum combined with the protective anodized layer contributes to improved fuel efficiency and performance. Moreover, the scratch and corrosion resistance of anodized aluminum enhance the durability of automotive parts, prolonging their lifespan and reducing maintenance requirements.
- Consumer Electronics: Anodized aluminum is commonly found in consumer electronics such as smartphones, laptops, and tablets. The sleek and modern appearance of anodized aluminum complements the design aesthetics of electronic devices. Furthermore, its scratch-resistant surface ensures that electronic gadgets maintain their pristine condition despite regular handling and use.
- Aerospace: Anodized aluminum is extensively used in aerospace applications for aircraft components, including fuselage panels, wing structures, and interior fittings. The lightweight yet strong properties of anodized aluminum contribute to fuel efficiency and payload capacity. Additionally, the corrosion resistance provided by the anodic layer is crucial for ensuring the safety and longevity of aircraft parts operating in harsh environments.
- Consumer Goods: Anodized aluminum is employed in various consumer goods, ranging from cookware and kitchen appliances to sporting equipment and furniture. The durability and aesthetic appeal of anodized aluminum enhance the functionality and visual appeal of these products, making them desirable choices for consumers.
Overall, anodized aluminum offers numerous benefits across diverse industries, including enhanced durability, corrosion resistance, and aesthetic versatility. Its widespread use underscores its importance as a versatile and reliable material for meeting the demands of modern manufacturing and design.
What is Anodized Aluminum?
Anodized aluminum refers to aluminum that has undergone a process called anodizing. Anodizing is an electrochemical process that enhances the surface properties of aluminum, creating a durable and corrosion-resistant finish.
During the anodizing process, the aluminum is immersed in an electrolytic solution and subjected to an electric current. This causes a controlled oxidation reaction to occur on the surface of the aluminum, forming a layer of aluminum oxide, known as the anodic layer. This layer is tightly bonded to the aluminum substrate, providing increased hardness, scratch resistance, and corrosion resistance.
Anodized aluminum is characterized by its ability to retain its appearance and structural integrity even in harsh environmental conditions. It is available in a variety of colors and finishes, making it a popular choice for architectural, automotive, consumer electronics, aerospace, and other applications where both aesthetics and performance are important.
What Are the Types of Aluminum Anodizing Processes?
There are several types of aluminum anodizing processes, each offering unique characteristics and benefits. The most common types include:
- Type I - Chromic Acid Anodizing (Chromate Conversion Coating):
- This process, also known as chromate conversion coating, uses chromic acid as the electrolyte.
- Type I anodizing produces a thin, dense, and corrosion-resistant oxide layer, primarily used for aluminum parts that require minimal buildup.
- It provides good adhesion for paints and adhesives but is less common due to environmental concerns regarding the use of chromic acid.
- Type II - Sulfuric Acid Anodizing:
- Sulfuric acid anodizing is the most common type of anodizing process.
- It involves using sulfuric acid as the electrolyte and operates at a lower voltage and higher current density compared to Type I anodizing.
- Type II anodizing produces a thicker oxide layer compared to Type I, offering improved wear resistance, corrosion resistance, and electrical insulation.
- It is widely used in various industries, including automotive, aerospace, and consumer electronics.
- Type III - Hardcoat Anodizing (Sulfuric Acid Anodizing with Lower Temperature and Higher Voltage):
- Also known as hardcoat anodizing or hard anodizing, Type III anodizing involves using higher voltages and lower temperatures compared to Type II anodizing.
- This process produces a thicker and denser oxide layer, typically ranging from 25 to 100 microns, resulting in significantly increased hardness and wear resistance.
- Type III anodizing is commonly used for applications requiring exceptional durability and abrasion resistance, such as military equipment, industrial machinery, and high-performance components.
These are the primary types of aluminum anodizing processes commonly used in industrial applications. Each type offers distinct advantages and is selected based on specific requirements such as hardness, corrosion resistance, wear resistance, and desired appearance.
Based on the concept of environmental protection and in order to comply with various regulatory requirements, YUH FIELD only has Type I and Type II manufacturing processes.
YUH FIELD is committed to environmental protection and complies with various regulatory requirements. It exclusively utilizes Type II and Type III anodizing processes for treating aluminum. Anodized aluminum, created through these processes, boasts enhanced durability, corrosion resistance, and aesthetic appeal.
What Are the Benefits of Anodized Aluminum?
Anodized aluminum offers several benefits compared to untreated aluminum or other surface treatments. Some of the key advantages include:
- Increased Durability: Anodizing creates a hard surface layer on the aluminum, making it more resistant to scratches, abrasion, and wear compared to untreated aluminum.
- Corrosion Resistance: The anodized layer provides excellent corrosion resistance, protecting the aluminum from oxidation and environmental factors such as moisture, chemicals, and salt spray.
- Enhanced Aesthetics: Anodizing can be performed in various colors, giving designers and manufacturers the flexibility to achieve different aesthetic finishes. The process can also enhance the natural metallic appearance of aluminum.
- Improved Adhesion: Anodized aluminum surfaces provide better adhesion for paints, adhesives, and other coatings compared to untreated aluminum. This allows for better integration into various applications and improved overall performance.
- Non-Toxic and Environmentally Friendly: Anodizing is a relatively environmentally friendly process compared to some other surface treatments. It does not involve heavy metals or hazardous chemicals, and it produces minimal waste.
- Thermal Insulation: Anodized aluminum has better thermal insulation properties compared to other metals, making it suitable for applications where heat dissipation or insulation is important.
- Electrical Insulation: The anodized layer acts as an electrical insulator, making anodized aluminum suitable for electronic components and applications where electrical conductivity needs to be controlled.
- Low Maintenance: Anodized aluminum requires minimal maintenance to retain its appearance and performance. It is easy to clean and typically does not require polishing or protective coatings.
Overall, anodized aluminum offers a combination of improved durability, corrosion resistance, aesthetics, and environmental benefits, making it a popular choice for a wide range of applications in industries such as construction, automotive, aerospace, electronics, and consumer goods.
What Are the Limitations of Aluminum Anodizing?
While aluminum anodizing offers numerous benefits, it also has some limitations and considerations to be aware of:
- Dimensional Changes: Anodizing can cause dimensional changes in the aluminum substrate, resulting in slight variations in part dimensions. Manufacturers need to account for this during the design and fabrication process.
Under normal circumstances, anodizing will slightly corrode the surface of aluminum products by about 0.01mm. After complete anodizing, the aluminum products will be covered with an oxide film of about 0.0025mm.
- Limited Color Options: While anodizing can produce a variety of colors, the range of available colors is somewhat limited compared to other surface treatments like painting or powder coating. Achieving specific custom colors may be more challenging and expensive.
In practical business collaboration, a notable challenge arises from the limited color availability at anodizing factories. This constraint stems from equipment limitations and the individual cost associated with each color variation. Unlike baking paint, where mixed color powder can be applied directly using a spray gun, anodizing demands a substantial amount of dyeing powder to be dispersed throughout the entire water tank for coloring a product. Consequently, unless the order volume is substantial, it is advisable to opt for colors already available at the anodizing facility. This approach ensures efficiency in production processes and minimizes costs associated with sourcing specific dyeing powders for custom color requirements. By aligning with the anode factory's existing color palette, businesses can streamline operations and optimize resource utilization while meeting project timelines and budget constraints effectively.
- Not Suitable for All Alloys: Not all aluminum alloys are suitable for anodizing. Alloys with high copper content, for example, may not anodize well and can result in uneven or undesirable finishes. It's essential to choose the right alloy for the desired anodizing outcome.
Speaking from experience, the 1000 series, 5000 series, and 6000 series are all alloys that are very suitable for anodizing, especially in dyeing, which can achieve even coloring effects. On the contrary, the anodized surface of ACD6 or ACD12 die-cast alloys is not as beautiful as the above alloys,and the distribution of the oxide film is also uneven.
- Limited Thickness Control: Anodizing typically results in a thin surface layer, usually ranging from a few microns to around 25 microns, depending on the specific process. Controlling the thickness of the anodized layer precisely can be challenging. In such cases, specifying the desired oxide film thickness range, such as 0.005 to 0.015mm or 0.025 to 0.035mm, to the anode factory becomes essential. Alternatively, if a minimum thickness is required, indicating 0.025mm or more can be beneficial. It's crucial to acknowledge that achieving thicker oxide film necessitates extended processing times. Therefore, clear communication regarding thickness preferences allows the anode factory to tailor the process accordingly, balancing the desired outcome with efficient production practices.
- Environmental Considerations: While anodizing is generally considered environmentally friendly compared to some other surface treatments, it still involves the use of chemicals such as sulfuric acid in the process. Proper waste management and environmental regulations must be followed to minimize the impact.
YUH FIELD is equipped with professional and comprehensive equipment for the treatment of wastewater, solid waste, and air pollution, all operated by licensed professionals. Our advanced treatment systems ensure effective management of various forms of environmental waste, including wastewater, solid waste, and air emissions. We are committed to responsible handling and mitigation of environmental pollutants, promoting sustainable practices and the preservation of ecological balance. With our expertise and dedication to environmental stewardship, we strive to protect natural resources and create a cleaner, healthier environment for present and future generations.
Despite these limitations, aluminum anodizing remains a widely used surface treatment due to its many advantages, including increased durability, corrosion resistance, and aesthetic appeal. Proper understanding of its limitations and careful process control can help optimize the outcomes of anodizing processes.
Where is Anodized Aluminum Used?
Anodized aluminum finds application in various industries and products due to its unique combination of properties. Some common uses of anodized aluminum include:
- Architectural Applications: Anodized aluminum is widely used in architectural applications such as building facades, window frames, doors, roofing systems, and curtain walls. Its durability, corrosion resistance, and aesthetic appeal make it a popular choice for exterior cladding and decorative elements.
- Automotive Industry: Anodized aluminum components are found in automotive applications such as trim, wheels, grilles, and body panels. The corrosion resistance and enhanced appearance of anodized aluminum make it suitable for both interior and exterior automotive parts.
- Aerospace and Aviation: Anodized aluminum is used extensively in the aerospace and aviation industries for aircraft components, including fuselage panels, interior fittings, structural parts, and aircraft skins. Its lightweight, corrosion-resistant properties are well-suited for aerospace applications.
- Electronics and Electrical Components: Anodized aluminum is utilized in electronic enclosures, heat sinks, printed circuit boards (PCBs), and electrical connectors due to its electrical insulation properties and thermal conductivity.
- Consumer Goods: Anodized aluminum is prevalent in consumer goods such as cookware, kitchen appliances, furniture, lighting fixtures, sporting goods, and handheld devices. Its scratch-resistant surface and decorative finishes make it desirable for these applications.
- Industrial Equipment and Machinery: Anodized aluminum is used in industrial equipment and machinery, including pumps, valves, hydraulic systems, and machine components. Its corrosion resistance and durability make it suitable for demanding industrial environments.
- Marine Applications: Anodized aluminum is employed in marine environments for boat hulls, marine fittings, railing systems, and offshore structures due to its resistance to saltwater corrosion.
- Medical Devices: Anodized aluminum is utilized in medical devices and equipment such as surgical instruments, dental tools, prosthetics, and diagnostic devices due to its biocompatibility and sterilization properties.
- Military and Defense: Anodized aluminum is used in military and defense applications for vehicle armor, weapon components, ammunition casings, and military hardware due to its lightweight, durable, and corrosion-resistant nature.
Overall, anodized aluminum's versatility, durability, and aesthetic appeal make it a preferred material choice across a wide range of industries and applications.
Conclusion
Anodized aluminum holds significant importance in modern manufacturing and design due to its versatile properties and wide-ranging applications. As a material, anodized aluminum offers exceptional durability, corrosion resistance, and aesthetic appeal, making it indispensable across various industries.
In architectural design and construction, anodized aluminum is a preferred choice for building facades, window frames, doors, and roofing systems. Its ability to withstand harsh environmental conditions while maintaining its appearance makes it an ideal material for exterior applications.
In the automotive sector, anodized aluminum is utilized for trim, wheels, grilles, and body panels. Its corrosion resistance and enhanced appearance contribute to both the aesthetics and functionality of vehicles.
In aerospace and aviation, anodized aluminum plays a crucial role in aircraft components such as fuselage panels, interior fittings, and structural parts. Its lightweight nature and resistance to corrosion are particularly advantageous in this industry.
Anodized aluminum also finds extensive use in electronics and electrical components, where its electrical insulation properties and thermal conductivity are highly valued. Enclosures, heat sinks, PCBs, and connectors benefit from the durability and reliability of anodized aluminum.
Consumer goods ranging from cookware and kitchen appliances to furniture and lighting fixtures often feature anodized aluminum for its scratch-resistant surface and decorative finishes. Its ability to maintain its appearance over time adds value to these products.
Industrial equipment and machinery utilize anodized aluminum for various components such as pumps, valves, and hydraulic systems. Its corrosion resistance and durability ensure reliable performance in demanding industrial environments.
In marine applications, anodized aluminum is favored for boat hulls, marine fittings, and offshore structures due to its resistance to saltwater corrosion. Its ability to withstand harsh marine environments makes it a preferred choice in this industry.
Medical devices and equipment benefit from anodized aluminum's biocompatibility and sterilization properties, making it suitable for surgical instruments, dental tools, prosthetics, and diagnostic devices.
Furthermore, anodized aluminum plays a vital role in military and defense applications, including vehicle armor, weapon components, and military hardware. Its lightweight yet durable nature provides essential protection in challenging environments.
Overall, the importance of anodized aluminum in modern manufacturing and design cannot be overstated. Its versatile properties make it an invaluable material across a wide range of industries, contributing to the development of innovative products and solutions.
YUH FIELD's dedication to sustainability extends to its waste management practices. The company employs advanced equipment for the treatment of wastewater, emissions, and soil contaminants, ensuring minimal environmental impact from chemical elements.
By prioritizing environmentally conscious production methods and investing in state-of-the-art waste treatment facilities, YUH FIELD strives to minimize its ecological footprint while delivering high-quality anodized aluminum products to its customers.