Understanding Aluminum Anodized Finish: Benefits, Applications, and Types
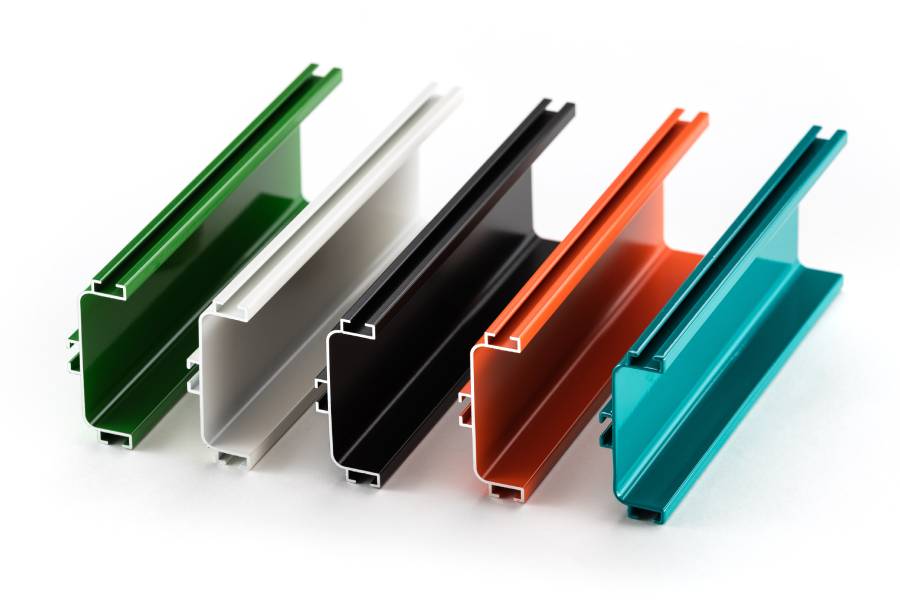
Aluminum is a popular material due to its lightweight and strength, but it is prone to corrosion and wear. To improve its durability, the anodizing process is used, creating a protective oxide layer on the surface. This layer not only enhances resistance to damage but also allows for aesthetic customization, making anodized aluminum a top choice in many industrial and consumer applications. In this article, we’ll explore the benefits, manufacturing process, common applications, and types of aluminum anodized finishes, with insights tailored to industrial buyers and engineers.
What is anodized aluminum?
Anodized aluminum refers to aluminum that has undergone the anodizing process, which involves creating a controlled oxide layer on its surface. This process enhances the aluminum's natural oxide layer, making it thicker and more durable. The anodized layer provides the aluminum with improved resistance to corrosion, wear, and various environmental factors, which is why anodized aluminum is widely used in industries where these properties are crucial.
What is aluminum anodized finish?
We can say that aluminum alloy in nature, through the action of time and air, will produce an oxide film, but the time required cannot be determined, and the distribution of the oxide film is uneven, long-term oxidation and erosion of the inside of the aluminum part, causing the aluminum part Fundamental damage. Aluminum anodized finish is to pass current, potion, and time, similar to forced oxidation, so that the pores of aluminum products produce a uniform film on the surface. This film not only has a protective effect, but is also resistant to wear and tear. Dyeing can be added in the process. It is of great help to industrial applications.
The Aluminum Anodizing Process
The anodizing process typically includes the following steps:
- Cleaning: The aluminum is cleaned in an alkaline or acid solution to remove surface contaminants.
- Etching: Optional step to give a matte or polished appearance.
- Desmutting: Removes any residual impurities from alloying elements.
- Anodizing: The aluminum acts as an anode in an acid electrolyte bath (commonly sulfuric acid) while current is applied.
- Coloring (Optional): The porous anodized layer can be dyed using organic or inorganic dyes.
- Sealing: The pores are sealed (typically in hot water or nickel acetate solution) to lock in color and enhance corrosion resistance.
Why are anodizing finishes important?
Anodizing finishes are crucial in enhancing aluminum's natural properties, making it more suitable for various applications. The anodized layer is integral to the aluminum, ensuring that it does not chip or peel. This layer provides significant protection against corrosion, wear, and environmental damage, making anodized aluminum ideal for both industrial and consumer applications. Additionally, the ability to dye the anodized layer in a variety of colors adds aesthetic value, allowing for creative and practical uses in architectural, automotive, and electronic products.
Common uses of aluminum anodized finish
Anodized aluminum is widely used across various industries due to its versatility and durability. Some common applications include:
- Electrolytic Capacitors: The anodized layer acts as a dielectric barrier, crucial for the function of capacitors.
- Anti-Corrosion: The anodized finish provides excellent resistance to corrosion, especially in harsh environments.
- Wear Resistance: The hardened surface created by anodizing increases the wear resistance of aluminum parts.
- Decorative Applications: The anodized surface can be dyed in various colors, making it popular for decorative purposes in consumer products.
- Coating or Electroplating Base: Anodized aluminum serves as a stable base for further coatings or electroplating.
- Electrical or Thermal Insulation: The anodized layer can act as an insulator in certain applications.
- Lubricant Absorption: The porous nature of the anodized layer allows it to absorb lubricants, enhancing its use in bearings and other moving parts.
Types of anodizing finishes
Different types of anodizing processes are used depending on the required properties of the finished product:
- Sulfuric Acid Anodizing: The most common type, providing a thick, durable, and colorable oxide layer.
- Hard Anodizing: Used for industrial applications requiring extreme wear resistance and corrosion protection.
- Chromic Acid Anodizing: Produces a thinner layer, often used in aerospace for its better fatigue resistance.
- Phosphoric Acid Anodizing: Primarily used as a pretreatment to enhance adhesion for subsequent coatings or bonding.
Finishing methods for aluminum
Beyond anodizing, other finishing methods can be applied to aluminum, including:
- Polishing: Enhances the surface’s reflective properties.
- Brushing: Creates a textured finish.
- Powder Coating: Adds a durable, colored coating on top of the anodized layer.
- Electroplating: Coats the aluminum with another metal layer for added properties like conductivity.
About aluminum anodized colors
Anodizing was originally developed for its functional benefits—corrosion resistance, rust prevention, and wear protection. However, the ability to dye the anodized layer has expanded its applications to include aesthetic purposes. Common anodized colors include black, gray, blue, red, gold, and brown, with black being the most popular in the market.
- Black Anodizing: Black dyes are typically based on a natural base color. Under normal lighting, differences in shades are barely noticeable, though special lighting or equipment might reveal slight variations.
- Blue Anodizing: There are several shades available, such as royal blue, water blue, and gray-blue, offering more options for customization.
- Other Colors: While a variety of colors can be achieved, they cannot be matched precisely using Pantone numbers due to the nature of the anodizing process.
Durability of anodized colors
The durability of anodized colors is a common concern, particularly in outdoor applications. As environmental issues gain attention, eco-friendly dyes are becoming increasingly popular. These dyes are designed to minimize harm to the environment and human health, making them a preferred choice for many manufacturers. However, the trade-off is that eco-friendly dyes may have lower outdoor durability and less color stability compared to traditional dyes.
FAQs
Q: Can anodized aluminum be repaired if it gets scratched?
A: Minor scratches on anodized aluminum can be polished out, but deep scratches may require professional refinishing.
Q: How long does anodized aluminum last?
A: With proper care, anodized aluminum can last for decades, depending on the environment and usage.
Q: Can anodized aluminum be recycled?
A: Yes, anodized aluminum is fully recyclable, and the anodizing process does not interfere with its recyclability.
Elevate your project with anodized aluminum
Choosing the right finish for your aluminum products can significantly impact their durability, performance, and visual appeal. Anodized aluminum offers unmatched benefits in corrosion resistance, wear protection, and aesthetic versatility, making it an ideal choice for a wide range of applications.
Ready to enhance your project with the best anodizing solutions? Contact us today to discuss your specific needs and discover how our anodizing expertise can bring your vision to life.
Don’t wait—get in touch with us now and let’s take your project to the next level with the perfect anodized finish!