What are Aluminum Extrusions?
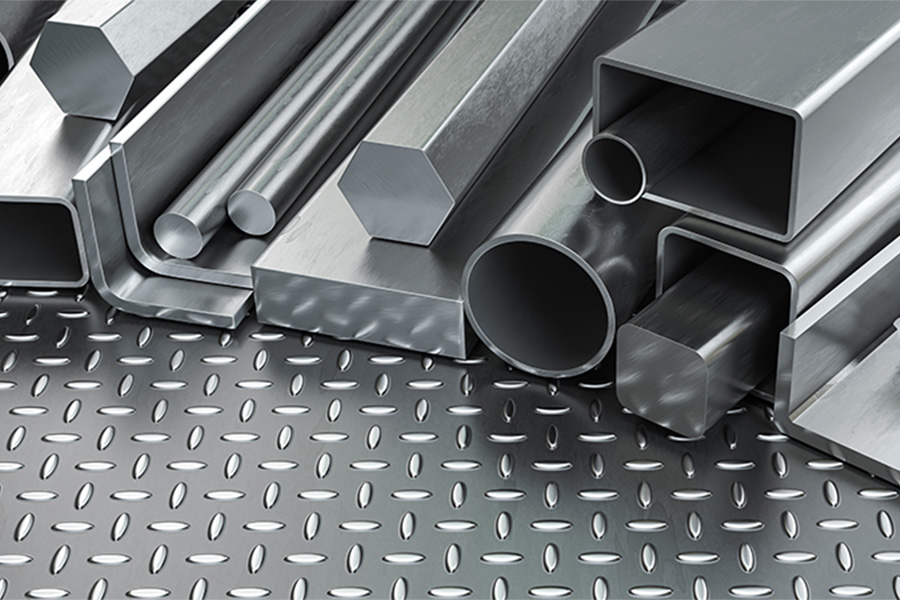
Introduction
This article will delve into the concept of aluminum extrusions and their significance across various industries. Aluminum extrusions represent a prevalent technology in manufacturing, boasting a broad spectrum of applications that underscore their paramount importance. Let's explore further.
What are Aluminum Extrusions?
Aluminum extrusion is a manufacturing process where Aluminum alloy is forced through a die with a specific cross-sectional profile. This process is commonly used to create a wide range of shapes and products, from simple rods and bars to complex cross-sections used in construction, automotive, electronics, and other industries. The extrusion process offers several advantages, including the ability to create complex shapes with high precision, excellent surface finish, and the ability to produce long lengths of consistent profiles.
The 6000 series, particularly alloys like 6061, 6063, and 6005, are indeed among the most commonly used materials for aluminum extrusion. Their popularity stems from their excellent extrusion efficiency, as well as their desirable properties such as good strength, corrosion resistance, and machinability. These alloys are extensively utilized in various industries for producing customized shapes and profiles, including home hardware, fitness equipment, building materials, industrial components, light bars, and more. Their versatility makes them indispensable in the manufacturing of a wide range of products where customized shapes and high performance are required.
The Process of Aluminum Extrusion
Before we mention the aluminum extrusion process, we must first mention the mold. An aluminum extrusion mold is a crucial component in the process of creating aluminum extrusions. An aluminum extrusion mold, also known as a die, is a specialized tool used in the extrusion process. Extrusion involves forcing an aluminum alloy material through a die with a predetermined cross-sectional shape. The goal is to shape the aluminum into a specific profile, such as a beam, tube, or other geometric forms.
Aluminum extrusion molds typically feature 2D designs, distinct from casting or injection molds. Once the mold is prepared, we heat the aluminum ingot to temperatures above 500 degrees to soften it. Then, utilizing pressure, we extrude the aluminum material through the mold to shape it according to the mold's design. Subsequently, a tensile machine is employed to pull the material, extending it into a long strip. Depending on the available factory space, extrusions may range from six to eight meters in some facilities, while others may reach ten to twelve meters.
The solid aluminum ingot, or blank, undergoes a transformation as it's subjected to substantial pressure and pushed through the porous aluminum extrusion mold. As it traverses the mold, it adopts the precise shape outlined by the mold's cross-section. Emerging from the die aperture, the extruded aluminum continues along a runout table. Throughout this journey, the aluminum undergoes significant shaping, gradually taking on the form dictated by the die. The result is a final extrusion that faithfully mirrors the shape of the die, ready to be utilized in various applications across industries.
After extrusion, the next step often involves heat treatment, also known as aging treatment. While aluminum can naturally gain hardness over an extended period when exposed to the air, this process can take six months or more. With heat treatment, however, the same results can be achieved in a much shorter timeframe, typically within six to eight hours. Additionally, heat treatment ensures a more uniform distribution of hardness throughout the aluminum material. This uniformity is essential for maintaining consistent quality and performance in the final product.
How to extrude aluminum into custom shapes?
Aluminum extrusion molds are categorized based on the cross-sectional shape of the extrusion they produce:
- Solid Molds: These molds create solid extrusions with a consistent cross-section throughout.
- Semi-Hollow Molds: These molds form extrusions with partially hollow sections.
- Hollow Molds: The most complex type, hollow molds produce extrusions with internal voids or hollow spaces.
Achieving customized shapes through mold design involves several key steps:
- Understanding Requirements: Understand the specific requirements for the customized shape. This may involve discussions with clients or stakeholders to determine their exact needs and specifications. striking a balance between customer needs and mold design limitations is crucial for an aluminum extrusion factory to provide cost-effective solutions to its customers.
- Designing the Mold: Based on the desired shape, design a mold that can produce it accurately and consistently. Considerations include the complexity of the shape, the material being used, and the manufacturing process. The design of the mold is closely related to the capabilities and specifications of the factory's aluminum extrusion equipment. The mold design should optimize material flow and minimize deflection during extrusion.
This involves considerations such as the shape and geometry of the die cavity, as well as the use of features such as fillets, radii, and draft angles to facilitate smooth material flow and reduce the risk of defects or distortion in the extruded profiles. The performance of the mold during extrusion is also evaluated. This includes monitoring parameters such as extrusion speed, temperature control, and pressure levels to ensure they are within acceptable ranges. Any issues or abnormalities observed during the extrusion process are noted for further investigation. - Manufacturing the Mold: Use machining or other manufacturing processes to create the mold according to the design specifications. Precision is crucial to ensure the mold accurately replicates the desired shape.
- Testing and Iteration: Test the mold with sample materials to ensure it produces the desired shape accurately and consistently. Make any necessary adjustments to the mold design or manufacturing process based on the test results. Once the mold is manufactured, it undergoes initial testing using sample aluminum billets. This involves setting up the mold in the extrusion equipment and running trial extrusions to produce sample profiles. These sample profiles are then evaluated for dimensional accuracy, surface finish, and other quality criteria.
- Production: Once the mold is finalized and tested, use it in the production process to create the customized shapes. Monitor the production process to ensure quality and consistency.
By following these steps, it's possible to design molds that can achieve a wide range of customized shapes for various applications. Each step requires careful attention to detail and collaboration between designers, engineers, and manufacturers to ensure the final product meets the required specifications.
What Are the Benefits of Aluminum Extrusions?
Aluminum extrusions boast several advantages, including but not limited to:
- Lightweight: Aluminum is a lightweight metal, and extrusions made from it offer good strength and stiffness while being lightweight. This characteristic reduces overall weight in various applications, enhancing transport efficiency and reducing costs.
- Corrosion Resistance: Aluminum exhibits excellent corrosion resistance, maintaining stability in diverse environmental conditions. This makes aluminum extrusions particularly suitable for outdoor, marine, and chemical environments.
- Machinability: Aluminum extrusions are easy to machine and shape, allowing for diverse design and production needs through processes like extrusion, cutting, punching, and welding.
- Excellent Thermal Conductivity: Aluminum possesses excellent thermal conductivity, making aluminum extrusions commonly used in applications requiring heat dissipation, such as electronic products and automotive engines.
- Recyclability: Aluminum is a recyclable material, allowing extrusions to be recycled and reused after their service life, promoting environmental protection and resource conservation.
- Aesthetic Appeal: Aluminum extrusions have smooth surfaces and attractive appearances. They can be decorated using surface treatments like anodizing, painting, and sandblasting to meet various application requirements.
In summary, aluminum extrusions offer advantages such as lightweight construction, corrosion resistance, recyclability, and more, making them widely utilized across diverse industries and applications.
Conclusion
Aluminum extrusion is a versatile manufacturing process used to create a wide array of shapes and products by forcing aluminum alloy through a die with a specific cross-sectional profile. This process offers numerous advantages, including the ability to produce complex shapes with precision, excellent surface finish, and the capability to create long lengths of consistent profiles. The 6000 series alloys, such as 6061, 6063, and 6005, are commonly used due to their extrusion efficiency and desirable properties like strength, corrosion resistance, and machinability.
Aluminum extrusion molds, crucial in this process, are specialized tools designed to shape aluminum into specific profiles. They come in various types, including solid, semi-hollow, and hollow molds, each suited to different extrusion requirements. Achieving customized shapes through mold design involves understanding customer needs, designing the mold, manufacturing it with precision, and conducting thorough testing and iteration to ensure accurate and consistent results.
The performance of the mold during extrusion is closely tied to the capabilities of the extrusion equipment, with factors such as pressure levels, machine size, and die heating and cooling systems influencing the process. Testing and iteration are essential stages to ensure the mold produces the desired shapes accurately and consistently, with adjustments made as necessary based on test results.
Aluminum extrusions offer numerous advantages, including lightweight construction, corrosion resistance, recyclability, and aesthetic appeal, making them widely used across industries. Their versatility and cost-effectiveness make them indispensable for applications ranging from construction to automotive and electronics. Overall, aluminum extrusion plays a crucial role in modern manufacturing, providing efficient solutions for customized shapes and high-performance products.
If you have any request for aluminum extrusion profiles, please feel free to contact us: https://www.yuhfield.net/en/contact